Home > Blog > Manual Cable Pulling vs. Mechanical Cable Laying: Key Methods in Power Construction In power engine
-
Haley
Hi there! Welcome to my shop. Let me know if you have any questions.
Your message has exceeded the limit.
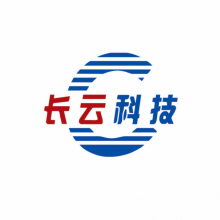
Manual Cable Pulling vs. Mechanical Cable Laying: Key Methods in Power Construction In power engine
2025-07-14 17:41:10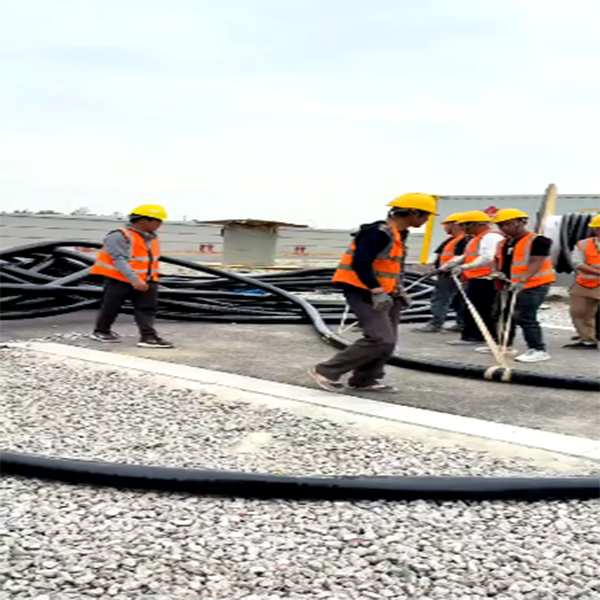
Manual Cable Pulling vs. Mechanical Cable Laying: Key Methods in Power Construction
In power engineering construction, cable laying is a fundamental yet critical task. With technological advancements, the methods have evolved from traditional manual pulling to modern mechanical laying. This article compares the two approaches, helping engineers select the most suitable option based on project characteristics.
Manual Cable Pulling: The most traditional method, relying on laborers to manually pull cables using simple tools (e.g., rollers). Suitable for short distances, small-section cables, and confined spaces where machinery cannot access.
Mechanical Cable Laying: Employs specialized equipment (e.g., winches) to provide traction, pulling cables via ropes or wire mesh. Ideal for long distances, large-section cables, and open areas like cable trenches or shafts.
Manual: Slow and labor-intensive, requiring multiple workers to coordinate and maintain uniform pulling speed.
Mechanical: Faster and continuous, with speeds up to 15 m/min, capable of handling multiple cables simultaneously without fatigue limitations.
Manual: Best for short, light cables in confined spaces (e.g., indoor wiring) or low-budget, small-scale projects.
Mechanical: Suited for long-distance, heavy cables in open areas (e.g., cable trenches), where precision and efficiency are required.
Manual: Risk of uneven pulling forces, cable twisting, and physical strain on workers.
Mechanical: Equipped with tension control devices and safety mechanisms (e.g., automatic load shedding) to prevent cable damage. Uses traction heads to distribute stress evenly across the cable.
Manual: Quality depends on worker experience, with challenges in maintaining consistent spacing, alignment, and bending radius.
Mechanical: Allows precise control of path, tension, and bending radius, ensuring compliance with standards (e.g., 35kV cables require specific laying angles).
Manual: Low initial investment but high labor costs for large projects, leading to overall inefficiency.
Mechanical: Requires upfront equipment costs but reduces labor expenses and shortens timelines, making it more economical for large-scale projects.
Regardless of the method, key steps include:
Traction Head Preparation: Use anti-twist devices to prevent cable distortion during mechanical laying.
Proper Fixing: Secure cables at endpoints, bends, and joints; use supports for vertical runs.
Bending Radius Compliance: Ensure minimum bending radius to avoid insulation damage (e.g., 15D for 35kV cables).
Redundancy Planning: Leave adequate slack at terminations and expansion joints for thermal expansion.
Advances include:
Automated Guided Systems: Reduce human error in complex layouts.
Hybrid Solutions: Combining manual and mechanical methods for challenging environments (e.g., indoor/outdoor transitions).
Smart Monitoring: Real-time tracking of tension and alignment to optimize performance.
Manual and mechanical cable laying each have distinct advantages. While mechanical methods dominate large-scale, high-precision projects, manual techniques remain valuable for niche applications. Engineers should evaluate project scale, timeline, and safety requirements to choose the optimal approach, leveraging technology to enhance efficiency and safety.
Safety Note: Always adhere to regulations, particularly ensuring proper tension control and worker training when using mechanical methods.
Haley
Sales Director
Zhengzhou Zhishi Changyun Technology Co., Ltd.
WhatsApp: +86 178 3831 1778
Email: changyunhaley@gmail.com
Tags: Manual Cable Pulling, Mechanical Cable Laying, electric cable conveyor
Popular Searches
- Alternative Energy Generators
- wind generator
- Permanent Magnet Generator
- Wind Turbine Generator
- Vertical Wind Turbine Generator
- Wind Power Generator
- Water Turbine Generator
- Horizontal Wind Generator
- turbine
- alternative energy
- hydro turbine generator
- windmill generator
- Turbine Power Generator
- Turbine Generator Set
- Permanent Magnet Alternator
- wind turbine